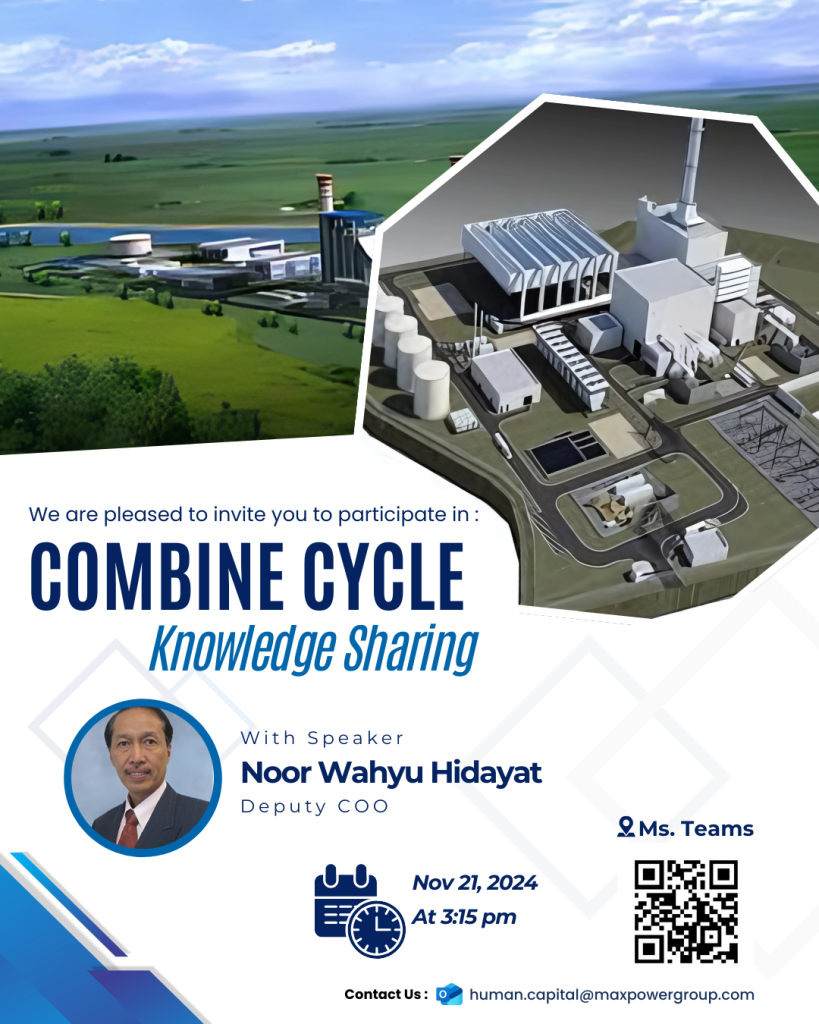
Maxpower Indonesia Hosts Knowledge Sharing Session on Combined Cycle Technology
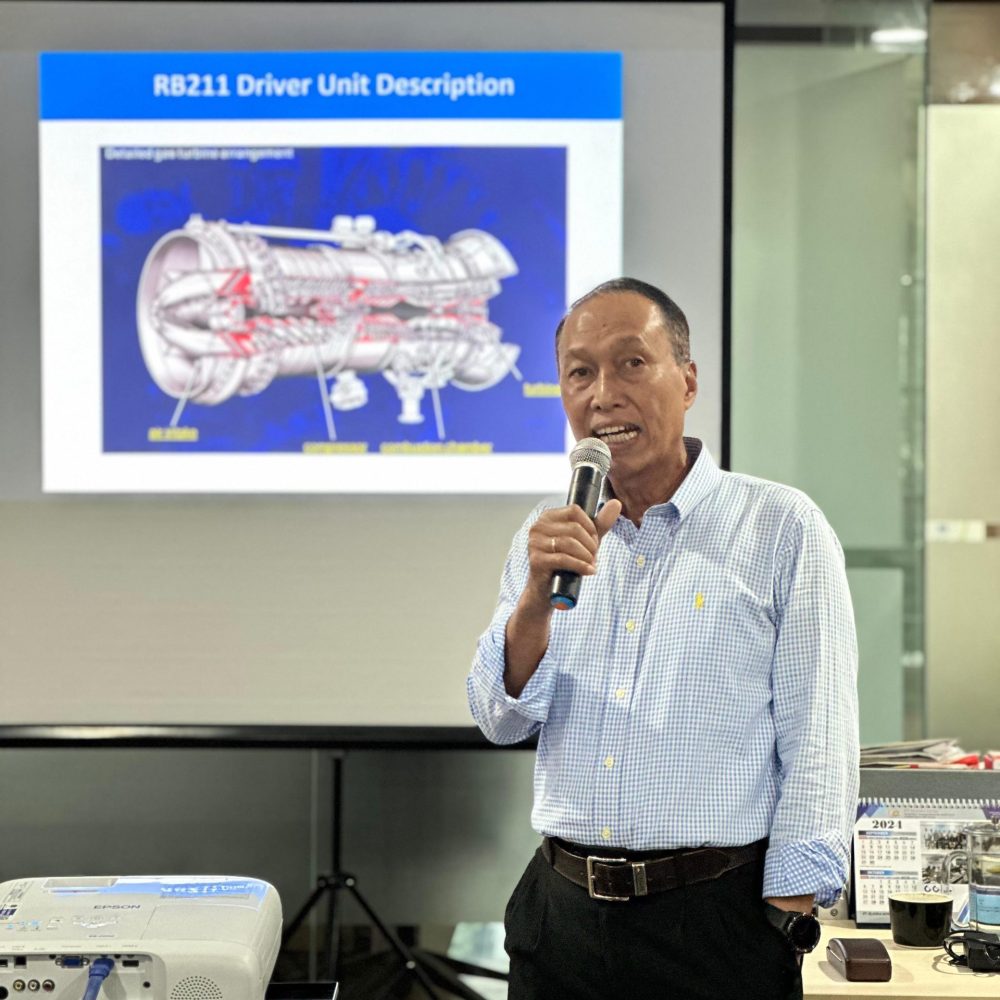
[Jakarta, November 21, 2024] – Maxpower Indonesia recently held a knowledge-sharing session on Combined Cycle Gas Turbine (CCGT) technology, with Mr. Wahyu, Deputy COO of Maxpower Indonesia, as the speaker. During this session, Mr. Wahyu shared valuable insights based on his experience with the implementation of combined cycle projects at Medco Power and Maxpower Indonesia.
Mr. Wahyu explained how the CCGT technology, which combines gas and steam turbines in a single cycle, enhances power generation efficiency by utilizing waste heat from exhaust gases to drive a secondary steam turbine. This approach not only improves energy efficiency but also reduces emissions and boosts overall performance. As part of its ongoing efforts to increase efficiency and output, Maxpower Indonesia has also undertaken a combined cycle retrofit, optimizing thermodynamic performance to minimize energy losses. The retrofit was implemented using a 2-2-1 combined cycle configuration, which increased plant efficiency from 35% to 52.4%, and reduced heat rate from 10,975 kJ/kWh to 6,864 kJ/kWh, resulting in a 37.5% efficiency improvement. This approach has proven effective in enhancing output while reducing energy consumption, providing significant benefits to the company’s operational performance.
Mr. Wahyu also discussed the chiller retrofit project carried out in 2007. With the site conditions in Batam having an average ambient temperature of 34°C, the initial power output from the gas turbines was limited to 27.5 MW (gross) per Gas Turbine Generator (GTG). To address this, an electrical chiller system was installed, resulting in an additional 8 MW gross of power output. This increased the total capacity of the two gas turbines from 55 MW to 63 MW. The investment for the chiller retrofit was USD 3.5 million, equivalent to USD 437/kW, significantly lower compared to the standard cost of SC at USD 600/kW.
Maxpower Indonesia also successfully implemented a retrofit for the Combined Cycle Power Plant (CCPP), with additional costs totaling USD 52.6 million, which is equivalent to USD 2,390/kW installed. The retrofit project reached its Commercial Operation Date (COD) on March 25, 2010. This retrofit significantly improved the power plant’s capacity and energy efficiency, aligning with Maxpower’s goal of providing more efficient and sustainable energy solutions.
Ensuring Minimal Disruption to Ongoing Operations for GTG Packages
Maxpower Indonesia emphasized the importance of minimizing disruptions to ongoing operations, particularly for the Gas Turbine Generator (GTG) packages. Regular maintenance is carried out according to scheduled intervals to ensure optimal turbine performance, with various types of inspections conducted at specific intervals:
- 8 & 16 K Maintenance Schedule (Class A Inspection)
This inspection includes checking the functionality of the gas turbine package system, performing a bore-scope inspection of the gas generator/power turbine, and reviewing the safety of equipment and control systems. It typically requires two Rolls-Royce field service personnel working 12-hour shifts over four (4) days, with a total downtime of 96 hours.
- 24 K Maintenance Schedule (Class B Inspection)
The Class B inspection includes all elements of the Class A inspection, plus the removal of the gas generator for Mid-Life Overhaul (MLO). This typically requires up to four Rolls-Royce field service personnel working 12-hour shifts over six (6) days. The total downtime is 144 hours (assuming the use of support units).
- 50 K Maintenance Schedule (Class C Inspection)
The Class C inspection includes all elements of the Class A inspection, plus the replacement of the gas generator for overhaul. This requires up to four Rolls-Royce field service personnel working 12-hour shifts over six (6) days. The total downtime is 144 hours.
- Class D Inspection
The Class D inspection includes all elements of the Class C inspection, plus the replacement of the power turbine for overhaul. This includes the replacement of D and T modules and other necessary components. It typically requires up to four Rolls-Royce field service personnel working 12-hour shifts over 10 to 12 days. The total downtime ranges from 240 to 288 hours (assuming the use of support units).
Conclusion
This knowledge-sharing session provided a deeper understanding for Maxpower employees about the benefits of CCGT technology, combined cycle retrofits, and effective maintenance practices to ensure smooth power plant operations. Maxpower Indonesia remains committed to delivering efficient and sustainable energy solutions, supported by the latest technology and meticulous maintenance management.